Summary
UC Berkeley process turns plastic waste into gases that are the building blocks for new plastics. The process, if scaled up, could help bring about a circular economy for many throwaway plastics, with the plastic waste converted back into the monomers used to make polymers.
UC Berkeley team develops process for breaking down polyethylene plastic bags into the monomer propylene. The monomers could then be reused to make polypropylene plastics. This would create a circular polymer economy for plastics, reducing the need to make new plastics.
In the new process, the expensive, soluble metal catalysts have been replaced by cheaper solid ones commonly used in the chemical industry. Continuous flow processes can be scaled up to handle large volumes of material.
The new catalysts avoid the need to remove hydrogen to form a breakable carbon-carbon double bond in the polymer. The two catalysts together turned a nearly equal mixture of polyethylene and polypropylene into propene and isobutylene.
Conk added plastic additives and different types of plastics to the reaction chamber to see how the catalytic reactions were affected by contaminants. Small amounts of these impurities barely affected the conversion efficiency, but small amounts of PET and polyvinyl chloride — PVC — significantly reduced the efficiency.
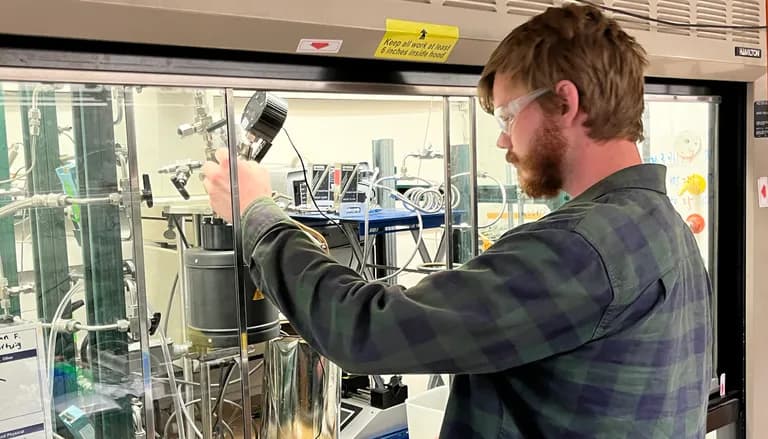